The 5S System : Sort, Set in Order, Shine, Standardize, Sustain.
The 5S System
Reading time : 5 min.
The 5S System.
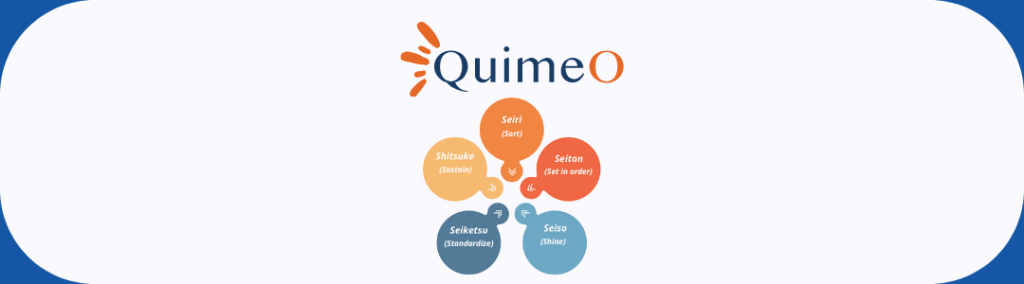
Summary : This article presents the 5S system, a method to organize workplace and enhance its efficiency. Besides, 5S promotes cleanliness, organization and standardization within the company, while improving productivity, safety and employee satisfaction. By implementing this system, organizations can streamline processes, reduce waste and create a positive work culture.
QuimeO – April 29th, 2025
1. Origin & Author
The 5S system, also known as 5S workplace organization, originated in Japan during the 1960s. This systematic approach was introduced in Toyota manufacturing plants by Taiichi Ohno, one of the precursors of Toyota Production System (TPS), in order to improve efficiency, organization and cleanliness in the workplace. On the other hand, the 5S was popularized in the USA by the book of Hiroyuki Hirano, 5 Pillars of the Visual Workplace (1990), and in France by the book of Takashi Osada, Les 5S (1993).
2. Definition
The 5S system is an approach to visual management and organization of the work environment. It is a set of five actions, each of these actions beginning with the letter “S” in Japanese: Seiri (Sort), Seiton (Set in Order), Seiso (Shine), Seiketsu (Standardize), Shitsuke (Sustain).
This system can be applied in a factory as well as at home. For example, it is possible to use the 5S method to organize offices or garages. Furthermore, this method can be implemented even at low or no cost, one only needs to take into account the right layout. This approach leads to identify errors as well as omissions thanks to the workspace organization. During its optimization, waste such as superfluous, unnecessary movements or excess stock are studied to be reduced at the most. In sumn, it is by respecting each action that the 5S can bring efficiency and save time while standardizing one’s organization.
3. Setting up
The implementation of the the 5S system requires a systematic approach and a collaboration involving all the employees. In fact, regular communication, training and feedback sessions are essential to ensure lasting success and continuous improvement. To implement the 5S, it is essential to follow these five steps in order:
- Seiri (Sort) : The first step consists in sorting or eliminating anything that is unnecessary in the workspace. This means to save only the essential items by establishing criteria to define whether an object is useful or not.
- Seiton (Set in Order) : The next step is to organize the necessary items in a methodical and logical manner. In this way, the more useful an item is, the easier it is to reach. In order to assign a specific place to each, it is possible to create visual controls such as “shadow boards” (boards with predetermined spots), labels or color codes. These practices enhance the quick search and access to necessary items.
- Seiso (Shine) : During this step, the workspace is carefully cleaned and maintained. This includes regular cleaning of surfaces, equipment and work areas to prevent the build-up of dirt and debris. In case of spread or contamination, it is important to identify and to eliminate the source. This helps to promote safety and improve the overall appearance of the workplace. Cleaning can also be useful for the maintenance thanks to the regular inspection and monitoring of the equipment by operators that can identify anomalies.
- Seiketsu (Standardize) : Standardization involves developing and implementing clear visual controls, standards, and procedures. All this to ensure that the first steps are properly followed throughout the organization.
- Shitsuke (Sustain) : The final stage consists in sustaining the improvements achieved in the previous stages. For this, it is essential to create a culture of discipline, continuous improvement and employee commitment to ensure that 5S practices are followed consistently in the long term. This helps to maintain an efficient and organized work environment. By monitoring and evaluating the implementation of the system, organizations can carry out periodic audits, provide feedback and address any deviations from established standards.
By combining these five steps, the 5S system reduces waste, improves productivity, enhances safety and creates a more pleasant working environment. It is important to note that the implementation process may vary according to the size of the organization, its sector of activity and its particular requirements. These steps must be adapted to meet the organization’s needs.
4. Conclusion
To conclude, the 5S system allows to favor and make continuous improvement a success throughout organizations while eliminating any type of waste (superfluous, excess stock, …). The input of 5S and visual management elements enables companies to improve operational performance and safety. Thus, organizations can reduce errors and create a visually appealing workplace that fosters a positive work culture by involving collaborators in improving their work environment. To make the implementation easier, it is possible to use online software.